Performance Days: The Latest Mega Trends
The focus on sustainable solutions was more present than ever with the return of the physical show in Munich
Back in its physical format after a two year absence due to the global Covid-19 pandemic, Performance Days, on April 27-28th, took place in a hybrid format. Retaining the wealth of information online, the trend forum, exhibitors and physical swatches made a much welcomed return. The show saw 2813 visitors, with 186 exhibitors in Munich, and 288 digital suppliers, together covering everything from base layers and membranes to trims for the active, outdoor and fashion industries. With LTP back exhibiting at the show and team in attendance, Alex Ingildsen, CCO at LTP Group states
“It’s great to be back at Performance Days in Munich. The show floor was brimming with excitement this year. It’s where the creative process begins and provides the ideal setting for us to meet new and exciting customers, suppliers and partners.”
Here we highlight some of the leading trends from this years show.
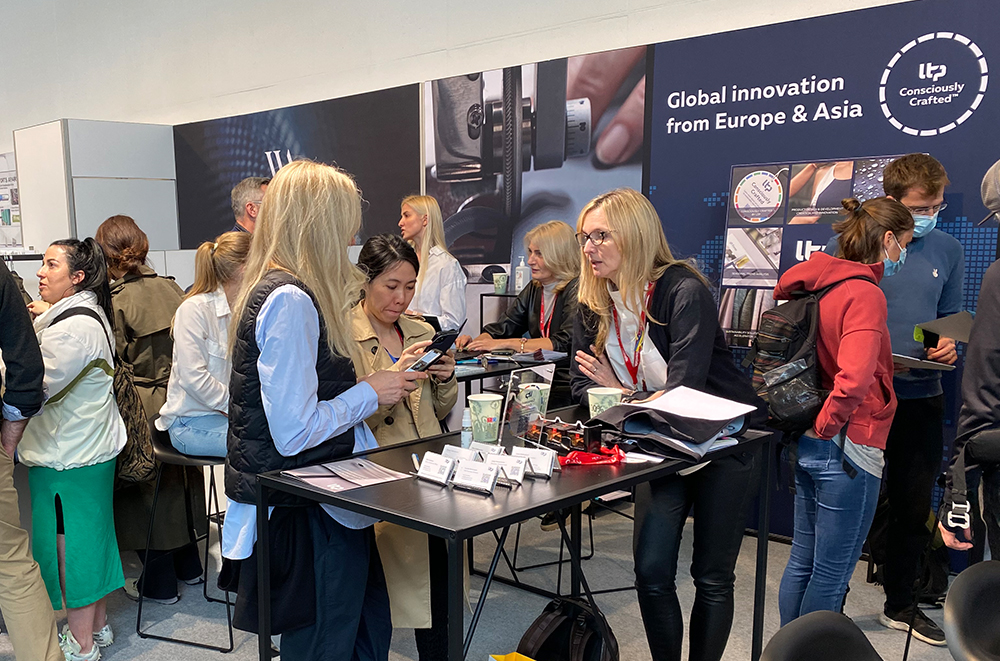
Carbon Neutral Innovation Dominates
Each season Performance Days highlights a Focus Topic, and this year was no different. With sustainability an ever present topic at the show, this season focused on the journey to carbon neutrality. With the majority of attendees understanding the ‘why’ and the ‘when’ of the importance of carbon neutrality, the show sought to answer how to achieve it.
As part of the Focus Topic, Performance Days highlighted material and fibre manufacturers that could demonstrate a lighter carbon footprint. Either by reducing, offsetting or capturing carbon.
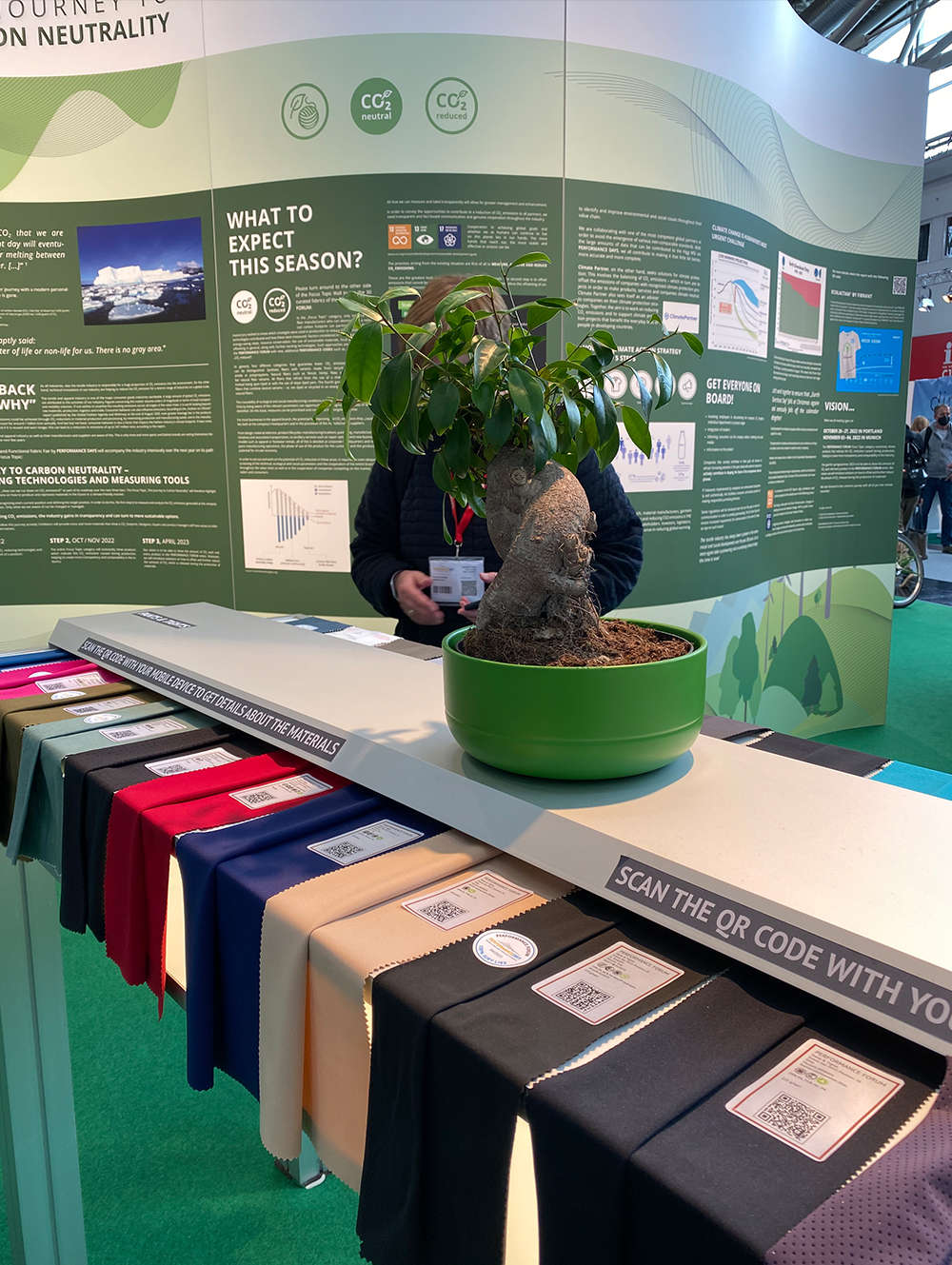
A key innovation, and selected by the Performance Days jury, was Shinkong’s certified carbon reducing yarns, highlighted for their functions in carbon neutrality and carbon reduction. The yarns are created through a biological process that captures and converts carbon, before recycling itinto ethanol through fermentation. The resulting 4-way stretch fabric offers a step in achieving net zero-emissions.
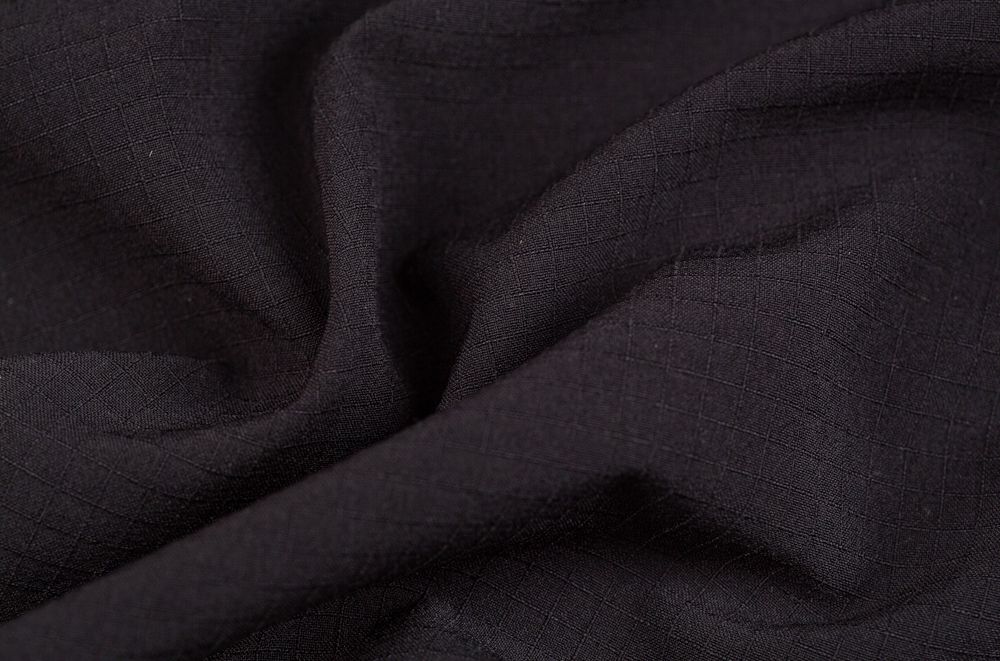
Everest’s carbon capture and utilisation PET double jersey was also shortlisted as a curated item. Working with similar technologies, they capture carbon emissions from steel mills and chemical plants, converting the carbon into raw material for polyester fibres.
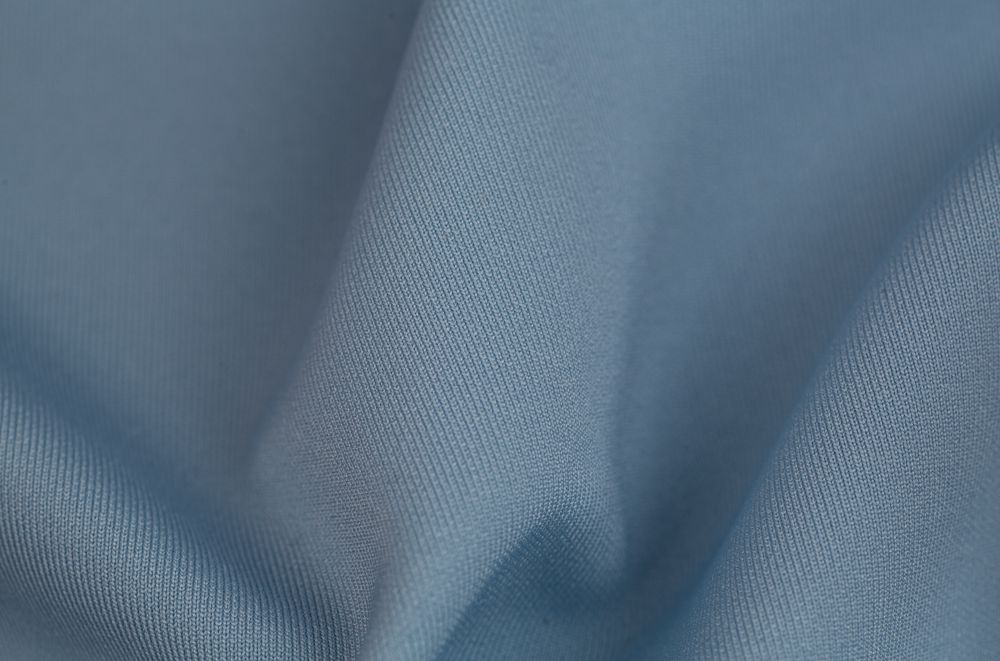
Elsewhere, LanzaTech have put the idea of carbon capture fabrics into practise with Lululemon, highlighting how this technology has the potential to be scaled. The US based bio-tech company, who use a similar method of carbon capture and conversion, announced in 2021 a partnership with Lululemon. The brand hopes their partnership, and the usage of the fibres, will help to deliver their goal of moving to a circular system by 2030.
A Bio-Natural Focus Continues
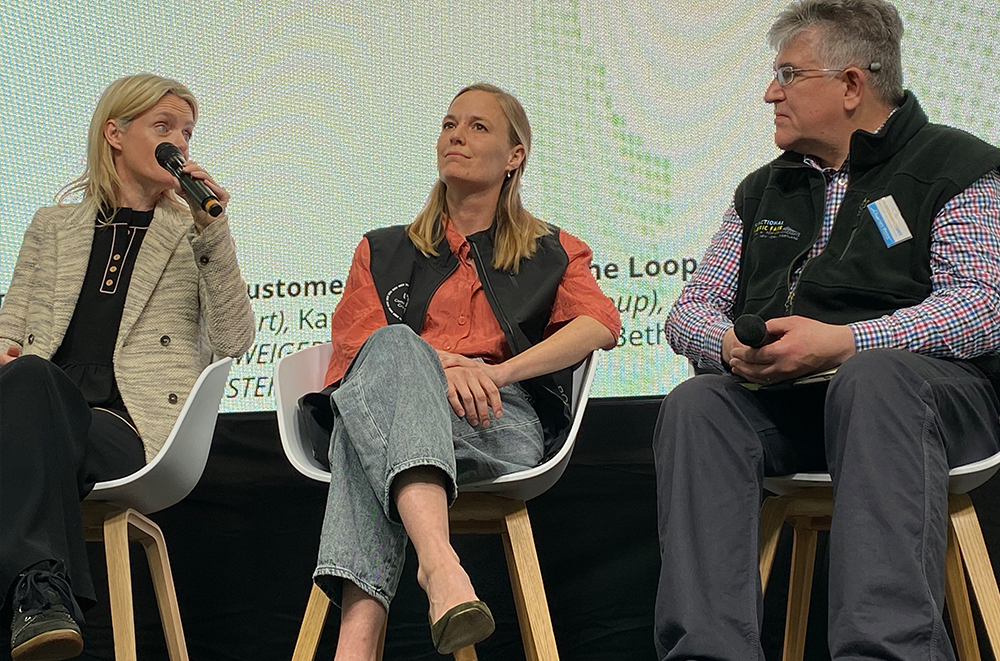
Sustainable innovations were also omnipresent outside of the Trend Forum. LTP’s Global Sustainability Manager Karin Simondon took part in a panel discussion with René Bethmann from Vaude, and sustainability expert Marianne Tochtermann to discuss the topic of Transparency and Closing the Loop of Circularity.
Elsewhere Trend Forecaster, Nora Kuhner covered the consumers desire to reconnect with nature and protect natural resources in her presentation on colour for the AW 23/24 season.
Much of the latest innovation was coming through in trims, including a range of alternative bio-based sources. In fabrics, biodegradability and natural stretch was also showcased this season.
Swedish based trim manufacturer, Wasa, was one of the leading exhibitors when it came to alternative plant based leathers. As part of the trend forum the supplier showcase patches made from either 50% leather, combined with cotton and polyester, or created from 100% pineapple. An advantage as the patch remains both natural and biodegradable.
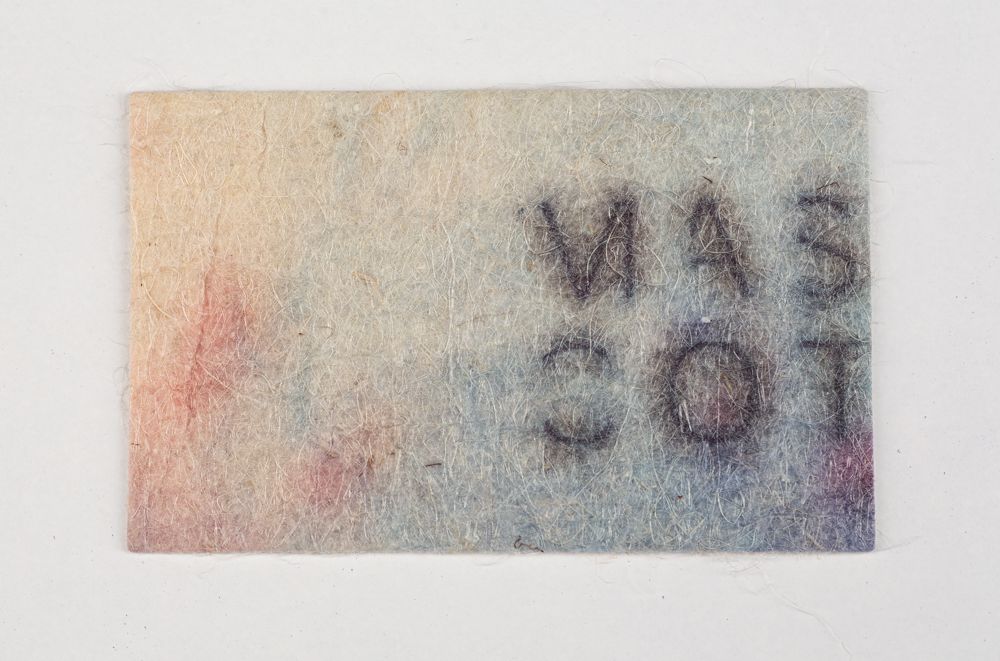
German based Nilorn were also exhibiting alternative leather patches, their Oeko-tex certified bio-based leather patch is created with 69% renewable resources, comprising 43% corn-polyols, 26% viscose and 31% PU. Another German trim manufacturer, Bitzer + Single, was also working with biodegradability. Their printed foil label used 100% organic and biodegradable PLA created from Biocartene, made from renewable resources.
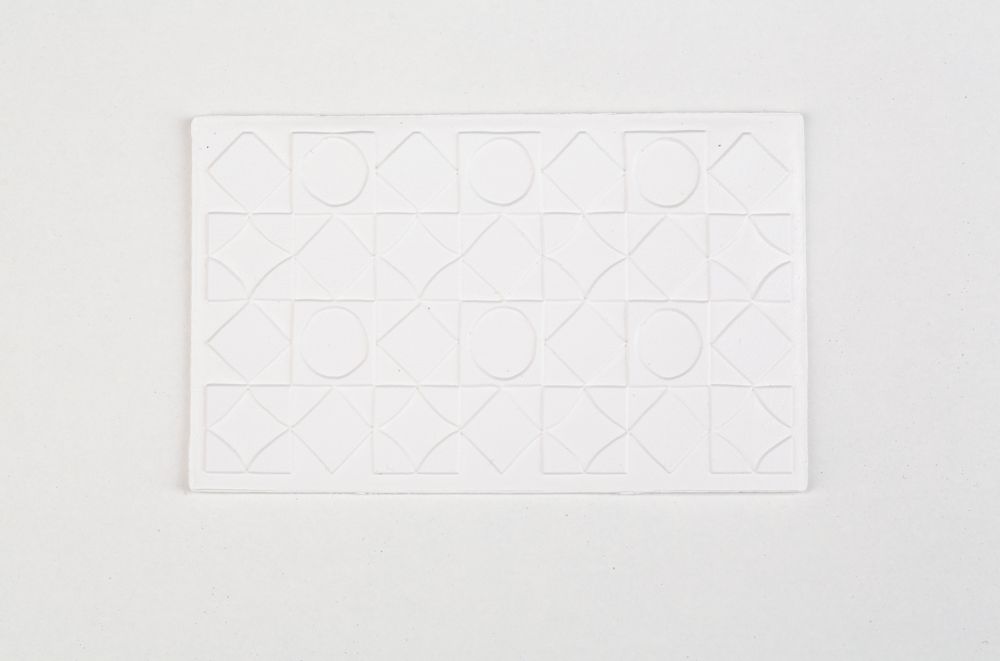
Conscious Colour Drives Innovation
A key area of importance for the active industries is the use of colour, but achieving it can often be wrought with chemical and environmental hazards. As consumers become more aware of these hazards, and express a desire to reconnect with nature, there is a growing interest and acceptance emerging around natural and low impact dye methods.
Dope-dying is nothing new to the active sphere, but has been gaining momentum over the last few years. The process involves adding pigments to the polymer solution before synthetic fibers are extracted. As part of the Trend Forum, Taiwanese mill Men-Chuen’s PES based mid-layer fabric was selected for its dope-dyed yarn. The material is created from 73% recycled PES collected from shoe waste, and combined with 27% virgin PES. The use of dope-dying also created a lower-carbon impact as less resources, including energy and water, are used than conventional dyeing.
Another Taiwanese mill, Axroma Technical Textile, also showed options in solution-dyeing. The Macintosh® Olefin yarn, which is used in their utility ripstop shell fabric, is solution dyed before being spun. The resulting material also uses a recycled TPEE membrane for waterproof performance. Selected for being both CO2 reducing and CO2 neutral, the fabric is also awarded Made in Green, and Standard 100 certifications from Oeko-Tex.
When it comes to a more natural based approach to colour, Korean based PLPTEX have used natural dyes in both their fabric dyes and prints. They’ve achieved this on woven recycled PES styles making it an ideal and innovative choice for the active and outdoor accessories markets.
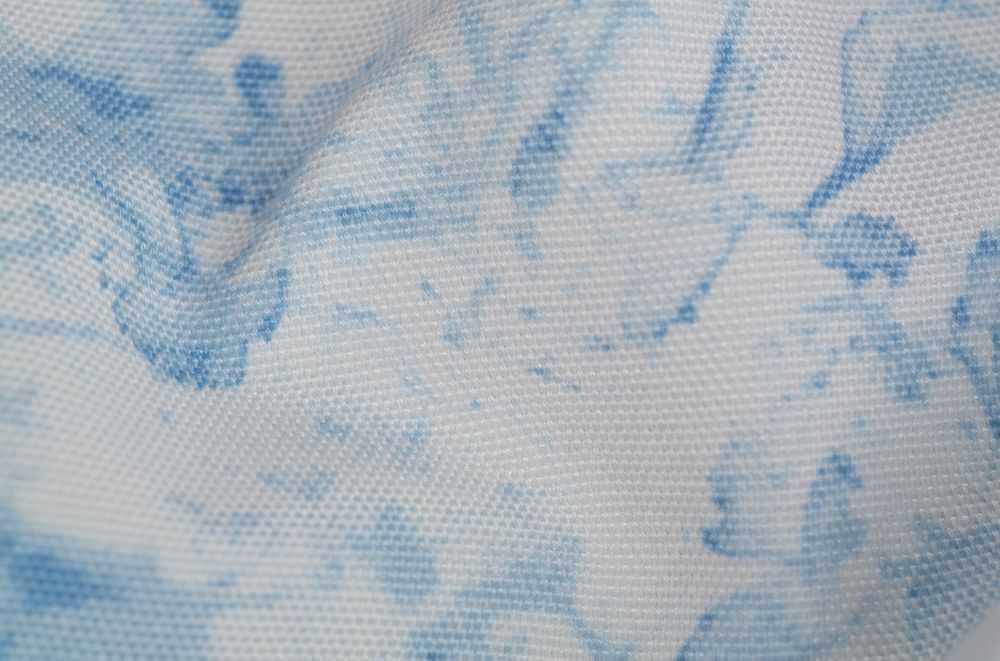
About LTP
LTP is a Danish owned garment manufacturer for +60 premium brands within active sportswear, cycling, outdoor, urban performance, performance running and organic & lifestyle apparel. LTP was established in 1991 and now spans two continents - Europe and Asia with 6 fully owned factories. Our European Innovation Centre is located in Kaunas, Lithuania and our Asian Innovation Centre is located in Ho Chi Minh City, Vietnam. We have a bluesign partner factory in all 4 countries where we operate (Lithuania, Ukraine, Belarus and Vietnam).
LTP consists of two divisions; LTP Garment and LTP Furniture producing in eleven fully-owned factories.