Outsourcing furniture production can be key to ensure high quality and sustainability
As the appetite for sustainable furniture builds, there has never been a better time for furniture brands to partner with an OEM specialised in sustainable production.
Be it the production of a single furniture component or entire pieces of furniture, outsourcing furniture production to an OEM partner is not only a smart move in terms of increased flexibility, benefiting from the expertise of specialised workers and freeing up resources to do what your business does best. It can also offer you a strong focus on both quality and sustainability – if the right OEM is chosen, that is.
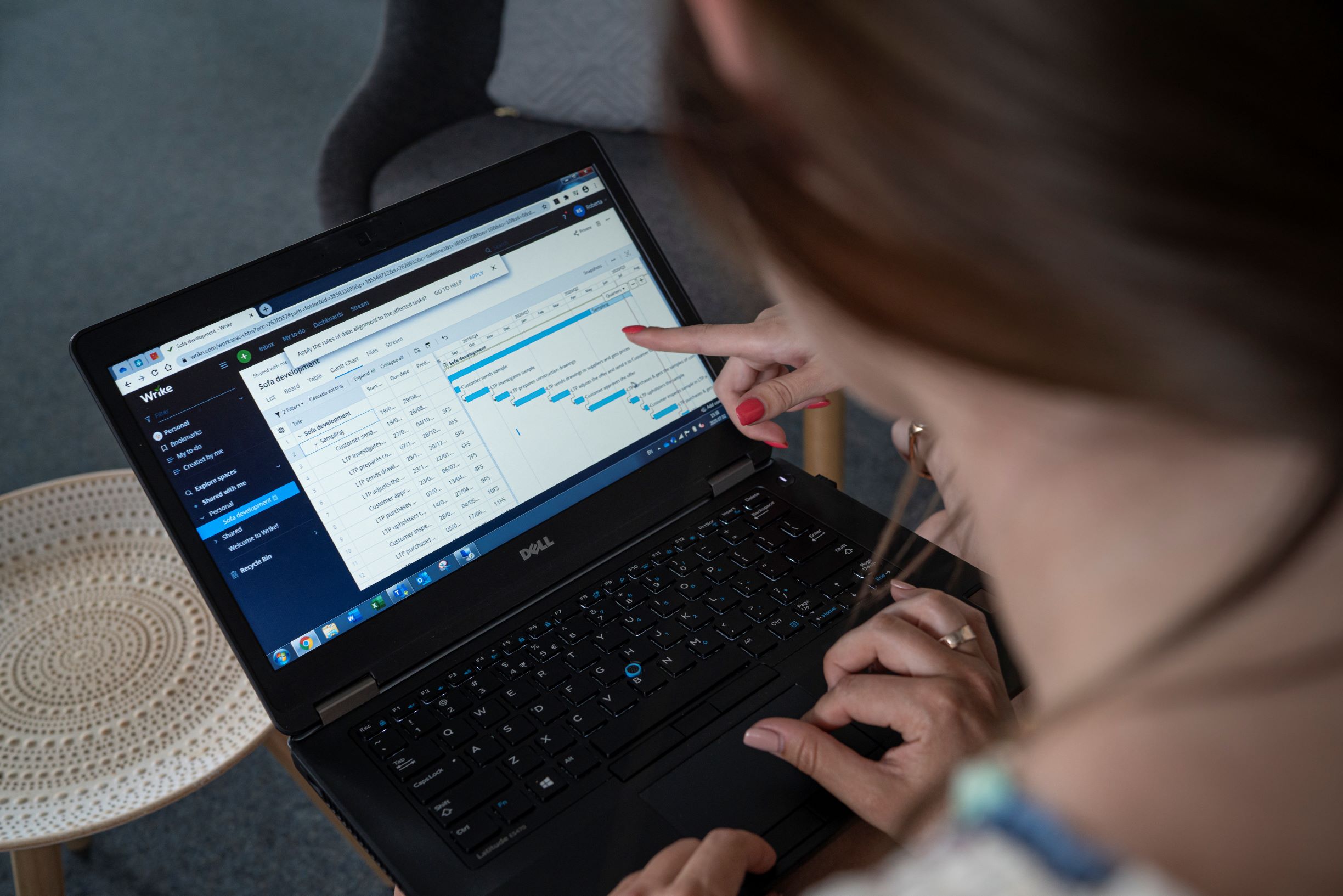
Sustainability is top of the agenda in the rapidly evolving residential and contract furniture markets – a trend which is fuelled by demands and requirements from end-customers, regulations, and investors. According to recent research from Deloitte, almost a third of end-consumers consider ethical and sustainability issues to be key drivers that can easily be a deal breaker and make them stop buying from brands due to related concerns. This calls for supply chain transparency. Customers are now asking: “Who made my furniture”? But to open for production transparency towards consumers, furniture brands need an OEM they can fully trust and rely on to make the right strategic choices when it comes to sustainability.
Sustainability is the new ‘quality’
What has been, for some time, nice-to-haves are becoming must-haves.
”Sustainability has become the new ’quality’. To be at the forefront, production companies must make investments and think long term.” says Karin Simondon, LTP Group’s Global Sustainability Manager.
She continues: “OEMs need to meet new environmental and social requirements, secure relevant certifications, and implement management and IT systems to support effective implementation of sustainability in daily operations. OEMs who look at sustainability as a way to increase the value of their operations, and as an integrated part of their know-how, will drive change across the furniture manufacturing industry. Because they are more specialised in what they do, that can also integrate sustainability much faster and effectively.”
By taking on a supply chain partner that – led by clearly defined sustainability priorities – has already acquired the relevant knowledge and planned for the right investments, furniture brands will be able to leapfrog sustainability and quickly gain competitive advantage.
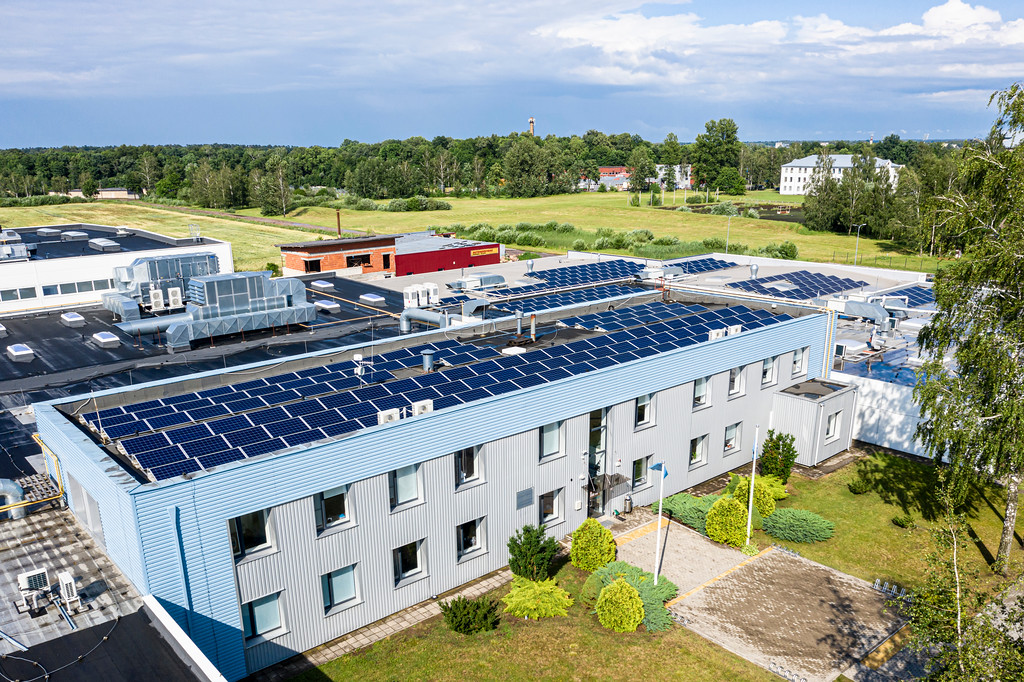
Walking the talk
Finding the right OEM partner that shares your quality and sustainability ambitions can seem like an overwhelming task, though, as sustainability can mean many things. Certifications are a manageable way to understand which quality and sustainability related requirements and standards an OEM has committed to meeting. Some good ones to look out for are FSC, which is catalyst for improved standards in forest management, STeP by OEKO-TEX, which certifies the long-term implementation of environmentally friendly production processes, social working conditions and optimum health and safety within the entire textile and leather production chain, and ISO-14001, the international standard for environmental management systems.
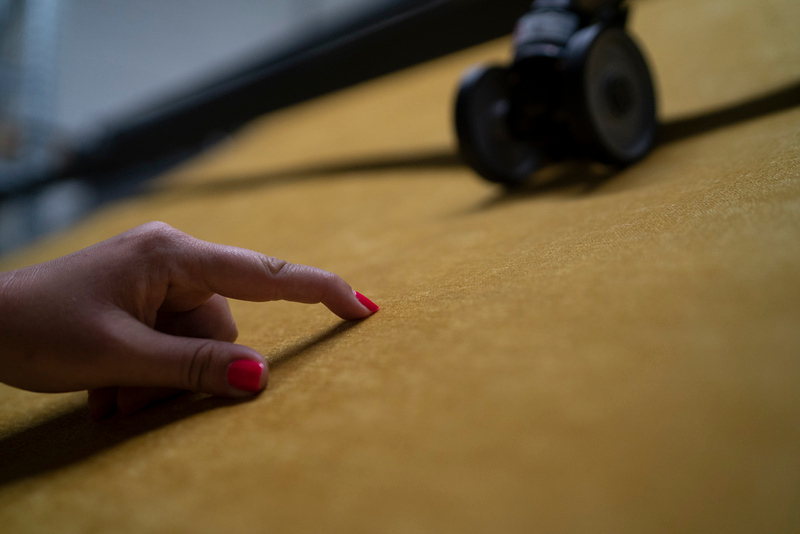
Automation and craftmanship go hand in hand
As a forward-thinking furniture brand, top-notch quality inspection is equally important in all parts of the process – product development, upholstery, assembly, packing, logistics. Keeping abreast with the ever-evolving technology and systems is a must to continually improve and achieve long-term customer satisfaction, and it is yet another reason to liaise with a production partner who has the most recent tools such as automated IT system-controlled technology, not to mention the most skilled experts in place. A combination that will be your route to long-term success.
About LTP
LTP Group is a production partner for demanding Sport & Outdoor Garments and Furniture brands with 10 fully-owned factories across 6 countries in Europe, Asia, and North America.
About the writer
Camilla writes about the contract and design furniture industry. She is particularly interested in how it is evolving – driven by the quest for more sustainablesolutions. https://www.linkedin.com/in/camillaoestergaardpedersen/