3D samples versus physical samples
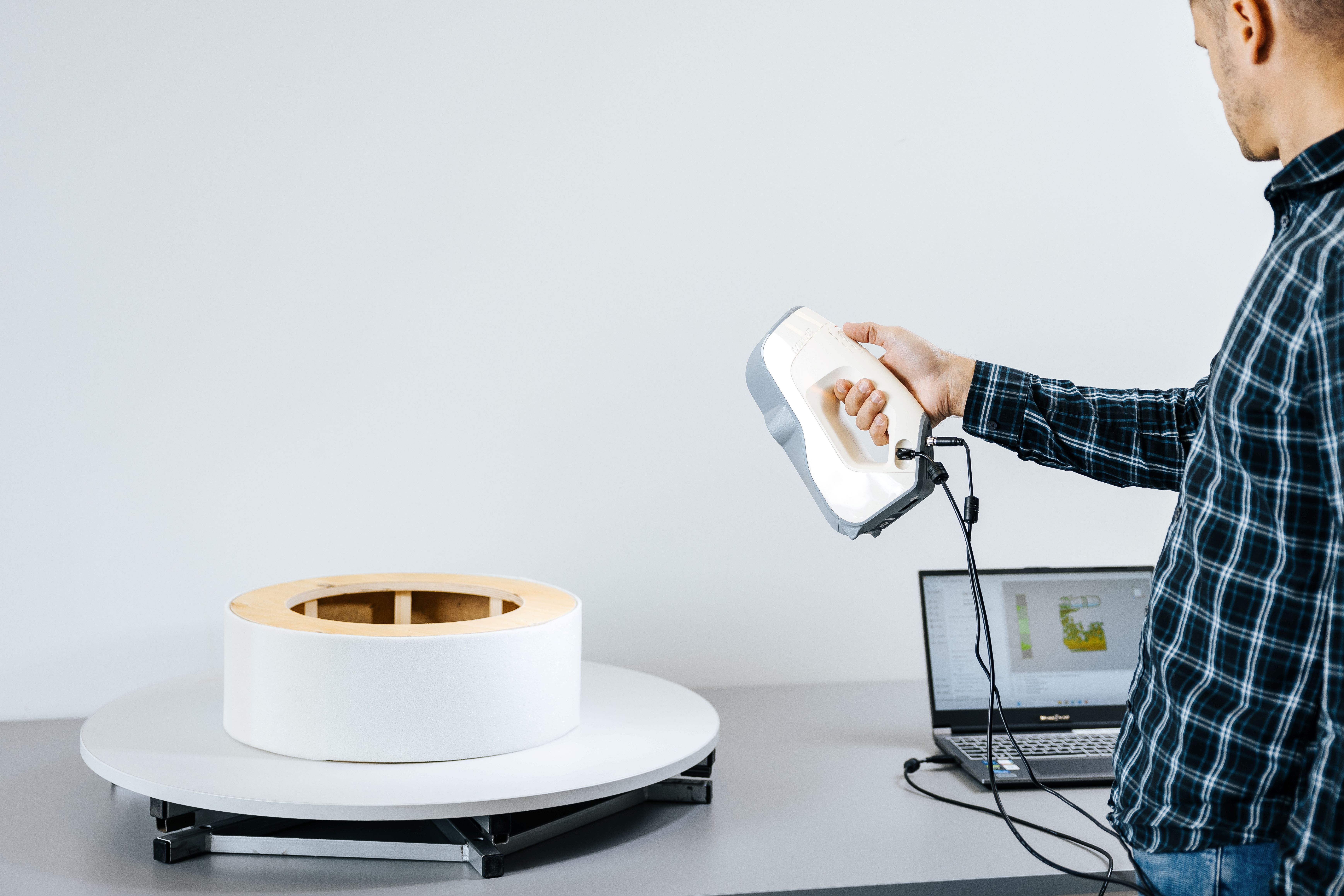
Developing both furniture and garments requires physical samples of the product for customers to accept the appearance of the product. To be faster and more efficient in our developing process we have invested in 3D technology within both our Furniture and Garment Divisions. A desired and sustainable benefit is that we reduce resource use and thereby enhance resource efficiency.
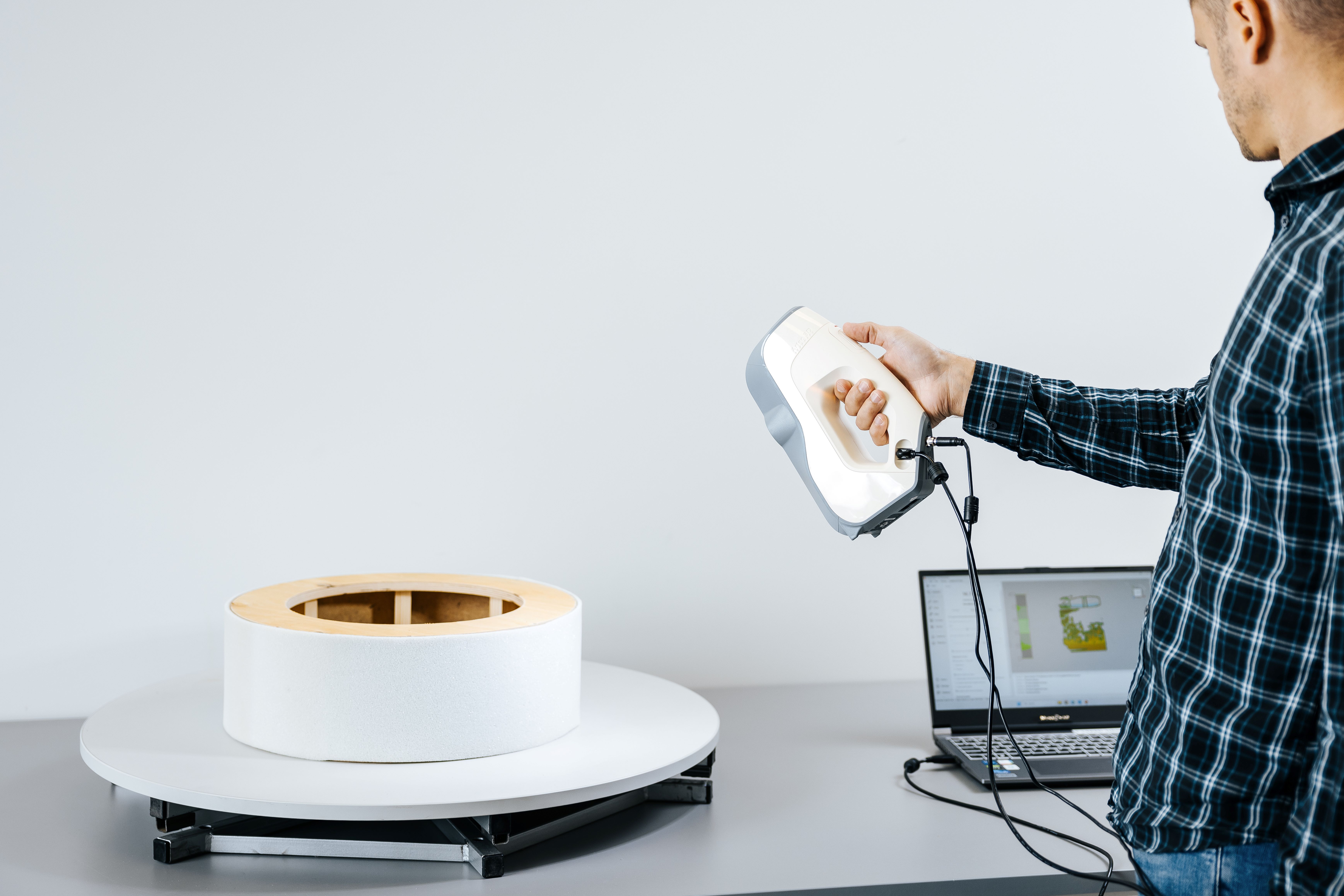
Developing a new product within Furniture optimized with 3D can reduce the number of physical samples from 5 to 2 in average. Appearance of the final product is everything when it comes to the iconic products that LTP Group manufacture, therefor the physical sample is inevitable, as how the materials work together and how the product feels in practice is possible to know only on a real product sample.
.jpeg)
The same applies within Garment, where it is normal to make several physical samples for the customer. Using 3D has reduced the number of samples as the look of the product can be finalized within 3D before making the first prototype. As the first prototype is already closer to the desired product it is the finalization of the appearance and feel of the product that determines the number of samples used. Savings with 3D samples is found in different stages of product development for example a 3D is made instead of the first prototype, a size set, a photo sample, or a preproduction sample. Making 3D samples before the first prototype saves about 30 % of all samples quantity. In 2023 we saved 7 % of all physical samples by using 3D.
3D can reduce the number of physical samples from 5 to 2 in average.
Making 3D samples before the first prototype saves about 30 % of all 3D samples quantity. In 2023 we saved 7 % of all physical samples by using 3D.